Plaster for Ceramics and Industry Use
There are various types suitable for different molding methods,such as slip casting, case molding, and original mold making.
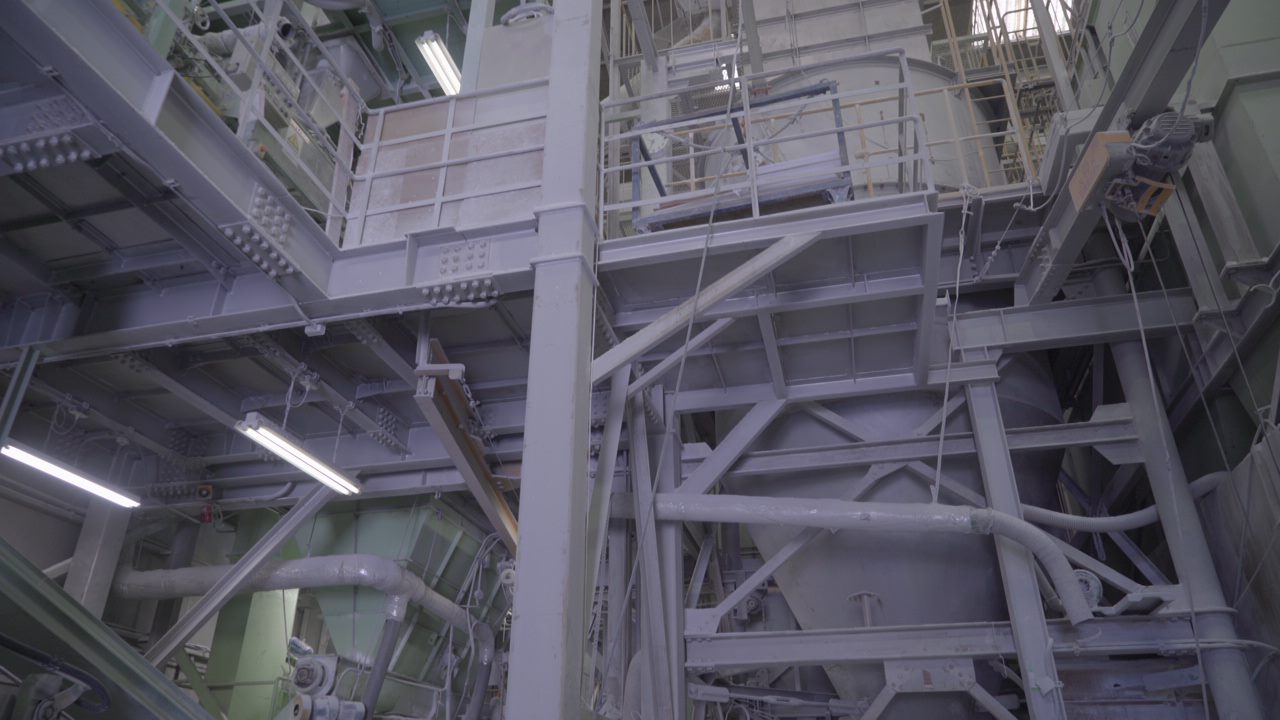
Product Lineup
For General Ceramics
These products can be used for roller machines and slip casting, among other applications.
-
Special Grade Blue M
Fully automatic roller machine use
General roller machine use -
Special Grade Green
Fully automatic roller machine use
General roller machine use
Pressure casting use -
Special Grade KATSU
General casting use
Pressure casting use -
Special Grade Calcined Gypsum Green HF
General casting use
Pressure casting use
Industrial model use -
Grade A
General casting use
Molding use
For Casting
Suitable for aluminum casting and glass casting.
-
Caster 8
Vacuum casting for zinc and aluminum
Glass molding
Caster 8 reinforced with fiber -
Caster Y
Vacuum casting for zinc and aluminum
Glass molding
SSS Caster / Gypsum for Glass Molding
-
- What is the basic process for glass molding using the caster?Open
-
The basic procedure is as follows
- 1.Create a Model (rubber, clay, wood, etc.).
-
2.Create a Cavity (pour casting gypsum
and demold)
*Reinforce by tying the surroundings with wire.
*Mixing with ceramic fibers or SUS fibers is also effective. - 3.Add Glass Powder to the wet gypsum mold (from baby powder size to fist size, standard 40 mesh per inch).
- 4.Dry overnight at 150-200℃.
-
5.Heat gradually to 830-850℃ over 5-6 hours, for large items, hold for 1-2
hours.
(Note:Depending on the technique and glass conditions, 680-1000℃). - 6.Cool down to room temperature over 3 days for small items and 4 days for large items.
- 7.Deburr and polish.
- 8.Completion.
-
- What are the methods and processes for using the caster?Open
-
1.Creation of the original model
- Materials used: wood, plaster, silicone rubber, metal, etc.
- Note: Wood and plaster molds require water absorption prevention treatment with lacquer or varnish.
- Note: For original models with undercuts, use elastic materials like silicone rubber.
2.Release Agent
- Materials: machine oil, Vaseline, machine oil mixed with kerosene + stearic acid
- machine oil + (0.1 – 0.5%) methylene chloride
- Note: Excess release agent can cause bubbles in the final product.
- Note: Insufficient release agent can cause adhesion to the original model.
3.Water Mixing Ratio
- 50% (100 parts plaster + 50 parts water)
- Note: Use drinking water for the process.
4.Mixing
- Methods: hand mixing, mechanical mixing, vacuum mechanical mixing
(vacuum
mechanical mixing is the most
suitable). Mix for 4-6 minutes. Insufficient mixing can lead floatation and reduce strength.
Approximately 850 milliliters of mold can be made from 1 kg of caster.
5.Pouring
- Pour the mixture quietly into the original model after mixing. During this process, apply vibrations to the mold or
use a brush to raise bubbles to the surface of the mold.
6.Demolding
- Perform demolding when the mold temperature reaches its maximum.
Using compressed
air can make removal
easier.
7.Drying
-
Leave the mold indoors for about 3 hours after
demolding.
- From room temperature to 100℃: 1 hour
- From 100℃ to 150℃: 1 hour
- From 150℃ to 250℃: 1 hour
-
Note: Drying time can vary greatly depending on mold size, ventilation
in
the drying machine, number of molds
in the drying machine, and their placement within the drying machine. - Note: It is crucial to measure the temperature at the center of the mold using a thermocouple.
- Note: The mold is considered dry when the temperature at its center exceeds 200℃.
8.Casting
-
- What is the method for aluminum casting?Open
-
- Notes1: For reduced pressure: Depending on the shape of the product, please attach the same type of decompression device to the upper part as well.
- Notes2: The appropriate reduced pressure is 24-30 mmHg (a vacuum gauge is required).
- Notes3: The effective decompression time is the first 30 seconds immediately after casting, and it should be maintained for 2-3 minutes in general.
- Notes4: There is also a method to apply decompression to the entire mold after casting.
- In the drying machine, gradually lower the mold temperature to about 80℃ over more than 3 hours.
- Adjust the vacuum gauge reading to around 20-30 cmHg before casting.
- Notes5: The demolding time should be at least twice as long as that for sand molds.